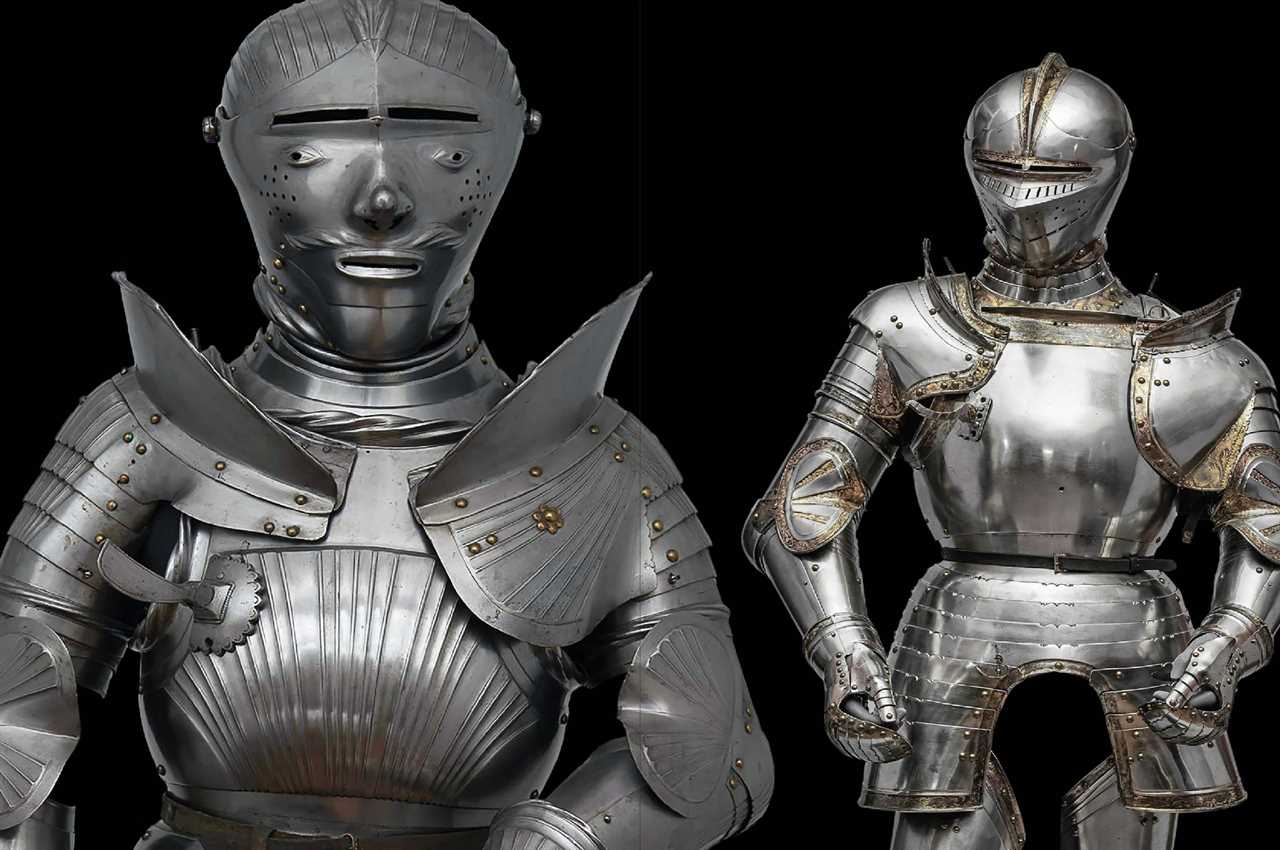
Steel plate armor is commonly associated with medieval times. However, studies reveal that the production of plate armor fully encasing the human body dates back to the early 15th century and reached its zenith a century later during the Renaissance.
Although developed initially for military purposes, so-called “suits of armor” took on different roles in society. Indeed, armor became a staple of social life and came to be viewed as a status symbol. Armor in fact performed various functions, and each suit was designed to be ideal for a specific purpose—whether for combat, tournaments, festivals or merely grand public events.
The Vienna Art History Museum (Kunsthistorisches Museum Wien) recently provided a highly detailed examination of the various forms, functions and types of armor in an exhibit entitled “Iron Men: Fashion in Steel” (Iron Men—Mode in Stahl) which ran from March through June, 2022 and showcased about 170 artifacts. The exhibit was Vienna’s first major exhibit about armor and sparked detailed studies of European steel plate armor by leading experts which provide useful insights to modern historians. Notably, the exhibit provided glimpses of rarely seen items from Vienna’s Imperial Armory, excellent examples of the flexibility of armor both as a military tool and as a statement ostentatiously declaring the wearer’s elevated social status.
“While some of these pieces were actually used in the bloodiest conflicts of the Middle Ages and Renaissance, others were worn at ceremonies like coronations and parades,” wrote Ronald S. Lauder, Director of Vienna’s Imperial Armory, in a museum book containing scholarly articles focused on the exhibition. “However all of them had one thing in common: breathtaking artisanship is present in every detail.”
The Origins of Steel Plate Armor
Suits of plated steel body armor were a European invention. Although commonly viewed as heavy and awkward by members of the general public today, they were in fact engineered to provide flexibility in combat as well as personal protection. Stefan Krause, curator of the Vienna Art History Museum, writes that a typical suit of steel armor weighed from between 40 to 60 pounds. He contends that wearing a suit of armor is comparable to firefighters, soldiers, or astronauts wearing protective equipment today—for example, the combat load (body armor, weapon, ammunition, water, supplies, etc.) carried by a typical Army or Marine infantryman in field operations today weighs 70 to 100 pounds or more! The Vienna museum’s suits of armor weigh substantially less than their modern counterpart gear, demonstrating that heavy gear can still be efficient, functional and offer mobility.
This rugged helmet (left) was made for a tournament game called the Kolbenturnier, in which mounted opponents fought to knock the crest from each other’s helmets; this plate armor (right) was designed for a jousting game called the Plankengestech. The latticed grandguard over the left arm formed the target area.
Steel plate armor was designed to withstand bladed, impact and bow-launched weapons from the early 15th to early 17th centuries, including polearms, swords, war hammers, arrows, crossbows and eventually early, primitive firearms. However, the advent over time of more powerful firearms featuring more efficient and reliable gunpowder, along with the development of increasingly-advanced military technology eventually rendered steel plate body armor obsolete.
Armor By Design
Armor production was overseen by master armorers, who honed their craft over many years and sold designs from workshops staffed by multiple employees. German and Austrian artisans in particular took armor production to a whole new level. With special focus on the intricacies of metal-working and engineering, they created workshops that were more like small factories where craftsmen worked in assembly lines and suits of armor were mass-produced—as well as custom made by special order. Notable armorers including members of the Seusenhofer family of Innsbruck, Austria and the Helmschmied family of Augsburg, southern Germany in addition to numerous armorers in Nuremberg, Germany, produced armor en masse and designed custom pieces for high-paying clients.
Master armorers were essentially the managers of these workshop “factories”—although responsible for the armor which carried their unique “brand,” they did not personally create every piece. They were however very involved in designing custom-made pieces by special commission.
Plate armor was created from sheets of metal cut and shaped by tools including shears, hammers and chisels. It was formed using various different shapes of anvils. Armorers also used molds. Steel sheets were usually worked cold, although sometimes bulges in the metal were removed through heating, according to Fabian Brenker in the Vienna museum’s exhibition book. Each piece of plate armor was specially crafted to fit and move in unison with other pieces.
Master armorers took care to ensure that all pieces fit together with precision and did not get stuck, chafe or open up awkward gaps exposing areas of the body when moving. Each piece had to be carefully aligned, and in fact no piece went into the final stages of production alone. Each element of the entire suit proceeded into the final stages of creation in unison. A single suit of steel plate armor could consist of as many as 200 individual pieces.
Fast-Produced, Not Just Mass Produced
Mass-produced armor was typically made of cheaper material and made available for common soldiers. It was not usually polished. Custom designed suits, often commissioned by aristocrats, were embellished and at times polished to create mirror-like surfaces. Polishing techniques included the use of large water-powered whetstones as well as smoothing using files. Extra polishing could be done using leather straps and emery mineral powder.
Noblemen such as Austrian Emperor Maximilian II provided master armorers with measurements to get the best fit from their steel suits (left); helmet design, an ancient art, could incorporate crests such as horns (center); master armorers could alter the color of metal and mimic intricate textile designs to create imposing looks (right).
Despite the meticulous craftsmanship needed to make good steel plate armor, expert armorers could accomplish their work with remarkable speed. Records show that Austrian armorer Jörg Seusenhofer, son of armorer Hans Seusenhofer and nephew of the more eminent armorer Konrad Seusenhofer, could produce an output of 90 pieces of mass-produced steel armor a week at his workshop, with his employees hammering 30 breastplates and backplates simultaneously per day. His famous uncle Konrad wrote in 1514 that he could produce two full suits of armor for a member of Italy’s famous Medici family within a mere two months with some added time needed for gilding. Konrad employed six masters and journeymen for detail work plus six or seven additional craftsmen for intensive labor, as well as four grinders and polishers, and support staff consisting of two day-laborers and one blacksmith.
Historical records indicate that smithing workshops in Nuremberg also used women to assist with polishing armor pieces and some detail-oriented tasks. Armor workshops often became generational family businesses.
Armor By “Mail Order”
Master armorers faced a unique challenge in taking the measurements of their clients. The best plate armor fit like a glove, encasing its wearer like a hard but fluid exoskeleton. Measurement was thus essential to producing a truly fine—and perfectly functional—product. However, the highest-paying clients were often royals or nobles who commissioned special suits from across long geographical distances throughout Europe. England’s King Henry VIII, for example, contracted Konrad Seusenhofer to produce a suit of plate armor, which when finished had to be delivered from Austria to England. Master armorers did not usually travel but made exceptions for royalty and heads of state.
Both armorers and their clients came up with creative ways to circumvent distance and get business done. Armorers sometimes sent paper templates for clients to try on, mark measurements on and return in a “mail-order” type of phenomenon. At other times clients sent pieces of their clothing to armorers. German armorer Konrad Richter, based in Augsburg, once used stuffing to fill clothes sent to him by a client to create a well-fitting steel suit. In one unique case, Emperor Charles V of Austria in 1526 created models of his legs using wax casts and molten lead and sent them to Augsburg to obtain custom-made greaves and cuisses from Kolman Helmschmied.
Embellishing armor became an art form unto itself. Armor pieces designed for aristocratic clients could be decorated using filing techniques, engraving, gilding, or riveting with copper alloy, and also painted—historical evidence suggests that painted pieces of armor were more common than previously realized.
The Many Uses And Variations of Armor
The appearance of a particular suit of steel plate armor largely depended on its intended use. Wealthy clients commissioned armor for public appearances at specific events such as festivals, ceremonies and tournaments. Some suits of armor served purely decorative functions, while others, such as tournament armor, were intended not only to be festive but functional in combat.
Armor also varied based on what type of combat it was intended for. For example, specific types of armor were made for jousting. Yet even jousting armor varied, Krause writes, depending on whether it would be used for high-impact jousting between individuals or jousting skirmishes between groups organized in “teams.”
This plate armor featuring a frowning visor (left) was likely worn for carnival processions; Austrian Emperor Ferdinand I commissioned armor for his son (right) featuring gilded eagles and matching garnitures allowing for 12 different modified versions of the suit.
Although it might seem like a finished suit of armor’s appearance was permanently fixed, it could actually be modified later. Clever master armorers sometimes developed upgrades called garnitures, which were essentially interchangeable pieces a man could swap out from his suit of armor depending on what activity he was engaging in. For example, pieces in the garniture set could be interchanged for tournament activities such as jousting or hand-to-hand combat on the battlefield. Garnitures were fashioned according to a cohesive design so that they did not appear mismatched when modifying a suit of armor.
A Matter of Prestige
Garnitures however were not the answer to every problem, and armor was incapable of being modified past a certain point. Men could outgrow their armor—particularly in early adulthood and middle age. Although master armorers could adjust suits of armor that did not fit their clients, or which needed some tweaking for comfort, it was simply impossible for even the best armorer to adjust a suit for significant alterations in size or weight. Thus, older adolescents would have had to forsake a favorite suit of armor after experiencing late growth spurts. Middle-aged men with any notable expanse in waistline would have been incapable of surreptitiously squeezing back into a lean suit of armor from their agile youth. Most often, men were required to obtain multiple suits of armor throughout their lifetimes. Commissioning new suits was always expensive, but for soldiers, knights and men who held leadership positions or influence in society, it was necessary.
Ceremonial armor could be shaped to imitate the fluid, curving intricacies of cloth, such as sleeves and skirts. Faux buttons and patterns could also be created, not to mention pictorial engravings that told stories in images across the wearer’s body. The creative possibilities were endless. South German Landsknecht mercenaries had a particular influence on fashion and also therefore steel armor. Seeking to distinguish themselves as an elite fighting force, they sported fancy clothing with dramatically puffed sleeves, bold colors and feathered hats. These mercenaries essentially sparked a bouffant fashion craze that spread throughout Renaissance Europe and quickly found its way into armorers’ workshops, and consequently into the portraits of nobles, military leaders and heads of state. Rulers and members of the aristocracy were quick to seize on the latest trends and show them off in the form of steel armor—it was a matter not only of style but prestige.
“Steel armor was a symbol of strength,” writes Krause. “Few other forms of representation symbolically brought out such an expression of the wearer’s prestige, his dignity, his political and military might—or at least his aspirations towards them.”
The Art of Helmets
In contrast to plate armor, metal helmets had already been decorated since practically time immemorial, and thus they were not as much of a novelty as steel plate armor. However, like plate armor, helmets adapted in form and function from the 12th century well into the Renaissance. With alternately ornamental or formidable appearances, steel helmets could appear as intimidating screens on the battlefield or whimsical headgear for festivals. Some common elements used to decorate helmets included plumes of feathers, horns, crowns, wings, or ancient family crests. Gold applique could also be used to create striking designs on helmets. The Landsknecht fashion trend during the Renaissance saw helmets made to appear like extravagant hats.
Helmets worn with steel plate armor are often presumed to offer minimal visibility to knights on the battlefield. While it is true that helmet visors provided narrow and limited fields of vision, additional vision was created by breathing holes in the visor. Larger breathing holes were ideal not only for vision but also to allow for inhaling more oxygen. Fewer and smaller openings in helmet visors did not allow for heat and carbon dioxide from exhalation to exit the helmet quickly, and limited breathing of oxygen could result in exhaustion, especially if the wearer was involved in intense physical activity. Historical records show that improving visor design was an issue and knights resorted to opening their visors in some instances despite the risk of exposing their faces in battle.
A prominent codpiece and billowing sleeves (left) feature in a 1523 creation by master armorer Kolman Helmschmied; gilded armor made for King Henry III of France (right) likely served a purely decorative function.
During the Renaissance, it also became fashionable to create costumes for festivals and tournaments harkening back to ancient times, or to faraway places. Noblemen sometimes cast themselves as heroes of ancient Rome or Greece, or even as mythological creatures, with classical or grotesque helmet designs.
How Armor Influenced…Fashion?
Although developed for military purposes, steel armor also revolutionized textile clothing. Men in Europe usually wore long tunics until about 1350, but a fundamental shift in men’s clothing style occurred during the middle of the 14th century as steel plate armor developed. The use of plated armor also required the use of close-fitting mail shirts. Soldiers and knights had already been wearing padded gambesons under mail or as an alternative to it in the 12th to 14th centuries. However, the development of more form-fitting steel armor pieces in the 14th century made tight padding beneath the steel too restrictive for movement. Quilted arming doublets with chainmail voiders or sleeves came into play, and from 1430 to 1470, padded material was restricted to protect the torso area. Tunics were thus no longer very practical and went out of style as shirts in general became shorter and tighter.
Another practical reason for this tectonic shift in outerwear was the fact that steel does not breathe and is not conducive to air circulation, thus trapping body heat. Doublets and lighter garments beneath the breastplate functioned to drain heat and perspiration and prevented wearers from becoming easily overheated.
Changes made not only to armor but everyday garments made the male silhouette more visible. While mail was initially worn to protect the lower body, detailed armor plates for the legs and lower body were engineered, including the codpiece.
The Humble But Proud Codpiece
The codpiece, known in German as the “modesty plate” (Schamplatte), has a unique history. It appears prominently in suits of armor and representations of Renaissance men. In her detailed study of codpieces in the Vienna museum book, Marina Viallon writes that figures wearing mail breeches with codpieces are depicted in stone funerary effigies from Germany from the late 14th century. Without padded codpieces, common infantrymen had minimal protection for the groin area in battle. The Landsknechts, whose influence on fashion might have eclipsed their military achievements, began wearing exaggerated codpieces to broadcast virility. The practice spread throughout the aristocracy of 15th century Europe—perhaps since noblemen wished to avoid the awkwardness of outwardly appearing less “virile” than commoners under their command.
Codpieces were adapted into steel armor pieces. Although worn during certain tournament activities, such as during single combat displays, they were never adapted for cavalry armor for practical reasons. Expensive to produce, they were sometimes decorated by gilding or engraving, and symbolized masculine power. “Worn like the prow of a ship, it was part of the body language of the ruling class, expressing confidence and authority,” writes Viallon.
Not Clunky, But Haut Couture
Whatever its purpose, every suit of armor constructed for a knight or highborn man was intended to reflect nobility of character. Concepts of knighthood influenced members of the gentry, with the result that knights and aristocrats—perhaps alternatively called “gentlemen”—were generally expected to be well-mannered, educated, and display social graces. They were different from common soldiers in that they were expected not to engage in undisciplined behavior such as public drunkenness. Brawling and disrespect towards ladies were also frowned upon. Thus, bespoke suits of armor created for high-ranking military men and members of the aristocracy were intended not only to symbolize power but to reflect greatness of spirit.
Steel suits of armor have been underestimated in modern times—incorrectly portrayed in popular films as clunky or dysfunctional relics from a bygone era. However, taking a closer look at the art, function and form of steel plate armor reveals much about not only the ingenuity of European artisans and craftsmen who developed it but also the high spirit of idealism that expressed itself in these sleek, strong bodies of metal.
this article first appeared in military history quarterly
See more stories
Subscribe now!
Facebook @MHQMag | Twitter @MHQMagazine
Did you miss our previous article...
https://lessonsbeyondthestory.com/lessons-learned/eye-in-the-sky